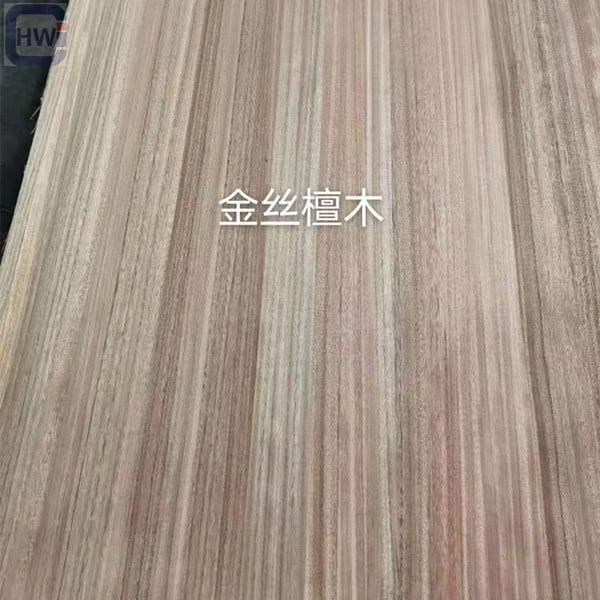
When it comes to marine construction or any project that involves exposure to water, the choice of materials is crucial. You need something that’s not just durable but can also withstand the harsh conditions of the sea, lakes, or even your backyard pond. That’s where structural marine plywood comes into play. In this article, I’ll be your guide as we delve into the world of structural marine plywood, discussing what it is, its applications, how to choose the right one, and much more.
What is Structural Marine Plywood?
Structural marine plywood, also known as marine-grade plywood, is a type of plywood specifically designed and manufactured to excel in water-based environments. Unlike regular plywood, which can easily warp, delaminate, or weaken when exposed to moisture, marine plywood is engineered to resist water and humidity effectively. It boasts exceptional durability, making it the preferred choice for applications where exposure to water is a constant challenge.
The Key Characteristics of Structural Marine Plywood
Structural marine plywood stands out due to its remarkable qualities, which make it ideal for marine and water-related projects:
- Water Resistance: This type of plywood is designed to withstand prolonged exposure to water without compromising its structural integrity. Whether submerged or in contact with moisture, marine plywood remains sturdy.
- Durability: Marine plywood is incredibly durable, capable of withstanding the wear and tear of marine conditions. It resists warping, rot, and pests, ensuring longevity.
- Strength: It offers a high level of structural stability, making it suitable for heavy-duty applications. Whether you’re building a boat, dock, or marine infrastructure, it can handle the load.
- Layers and Glue: Marine plywood is typically constructed with several layers of high-quality wood veneers, bonded together with waterproof glue. This layering and bonding process contributes to its strength and water resistance.
Applications of Structural Marine Plywood
Marine plywood’s impressive features make it versatile and valuable for a wide range of applications, both in the marine industry and beyond. Here are some common uses:
1. Boat Building
Marine plywood is synonymous with boat building. It’s the primary choice for constructing the hull, decks, and interior of boats. Its water-resistant properties ensure the vessel’s longevity and structural integrity even when exposed to constant water and marine conditions.
2. Docks and Piers
Docks and piers demand materials that can endure not only the forces of the water but also heavy loads. Structural marine plywood is the go-to choice for building these waterfront structures, providing stability and durability.
3. Outdoor Furniture
If you’re planning to craft outdoor furniture for your patio, garden, or pool area, marine plywood is an excellent choice. Its ability to resist moisture and pests ensures your furniture will withstand the elements for years to come.
4. Bathroom and Kitchen Cabinets
For areas where high humidity is a concern, such as bathrooms and kitchens, marine plywood is a smart choice for cabinet construction. It prevents warping and delamination, ensuring the longevity of your cabinets.
5. Playhouses and Treehouses
When building playhouses and treehouses for your children, you’ll want to use materials that can handle the weather. Marine plywood keeps these structures sturdy, safe, and fun for your kids.
6. Outdoor Signage
Structural marine plywood is a great choice for outdoor signage. Its weather-resistant properties ensure your signs remain intact and readable for a long time.
Choosing the Right Structural Marine Plywood
Selecting the right marine plywood is critical to the success of your project. Here are the key factors to consider:
1. Plywood Grading
Marine plywood comes in different grades, with A-A being the highest quality. It’s important to choose the grade that matches your project’s requirements. A-A plywood has no knots or voids, making it ideal for high-end applications, while lower grades may have slight imperfections.
2. Thickness
The thickness of the plywood is determined by the structural requirements of your project. Thicker plywood is more robust and can handle heavier loads, but it’s also heavier and more expensive. Consider the needs of your project to choose the right thickness.
3. Type of Wood
Marine plywood can be made from various wood species, including meranti, okoume, and Douglas fir. The choice of wood impacts the plywood’s durability and appearance. Meranti and okoume are popular choices due to their water-resistant properties.
4. Quality of Glue
The glue used to bond the layers of plywood is crucial. Look for plywood that uses high-quality, waterproof glue to ensure long-lasting performance in wet conditions.
Frequently Asked Questions
Q1: Can I use regular plywood instead of marine plywood for outdoor projects?
A1: While regular plywood is suitable for some outdoor applications, it’s not recommended for projects that involve constant exposure to water. Marine plywood’s water resistance and durability make it the better choice for such projects.
Q2: Is marine plywood more expensive than regular plywood?
A2: Yes, marine plywood tends to be more expensive than regular plywood due to its specialized manufacturing process and superior qualities. However, the added cost is justified by its longevity and performance in water-based environments.
Q3: How do I maintain and protect marine plywood in outdoor applications?
A3: To ensure the longevity of marine plywood in outdoor projects, apply a quality exterior finish or paint to seal the wood and protect it from the elements. Regular maintenance, such as resealing and checking for any signs of damage, is also essential.
Q4: Can marine plywood be used for interior applications?
A4: Yes, marine plywood can be used for interior applications, especially in areas with high humidity or moisture, such as bathrooms and kitchens. It’s a durable choice for cabinets and other indoor structures.
Q5: Is marine plywood the same as pressure-treated plywood?
A5: No, marine plywood is not the same as pressure-treated plywood. Pressure-treated plywood is infused with chemicals to resist rot and pests, while marine plywood relies on its construction and type of wood to provide water resistance.
Conclusion
In the sea of plywood options, structural marine plywood emerges as a reliable and durable choice for projects that face constant exposure to water. Its exceptional water resistance, strength, and versatility make it a top pick for boat building, docks, outdoor furniture, cabinets, and much more. By choosing the right grade, thickness, wood type, and paying attention to glue quality, you can ensure that your marine plywood project stands the test of time. So, when you’re ready to embark on your next marine or water-related project, look no further than structural marine plywood to get the job done with excellence.
Whether you’re building a boat, revamping your waterfront deck, or crafting a sturdy outdoor playhouse for your children, marine plywood is the treasure trove of materials that ensures your project’s success. Uniquely designed to combat the challenges of a water-based environment, it is your go-to solution for strength, durability, and long-lasting beauty in the face of nature’s elements. So, unlock the potential of your next water-centric project with structural marine plywood – a material that truly embraces the power of wood in the water.
Post time: 14 10 月, 2023